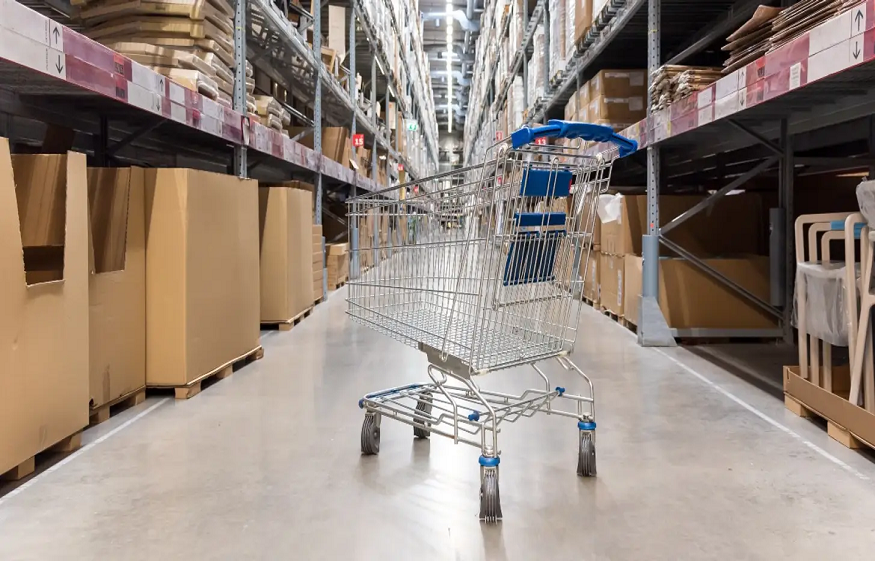
Choosing a proper inventory planning solution for your business is not a simple task. The quicker your company grows, the more difficult it gets to manage the inventory. That is why setting the right foundation from the beginning is essential. Let us learn more about the inventory planning techniques, benefits, and challenges.
What Is Inventory Planning?
Inventory planning is an integral part of supply chain management. It is the method of keeping track of stock levels and the movement of goods, such as delivering raw materials to the manufacturers for manufacturing and finished goods to customers for fulfilling orders. Inventory planning is essential for assisting businesses in reducing costs, enhancing cash flow, and increasing profitability. Inventory planning assists companies in determining how much inventory should be replenished and when. Inventory planning systems track inventory from purchase to the sale of goods.
Why Is Inventory Planning Essential?
When the inventory is optimized correctly, the rest of the supply chain becomes functional and efficient automatically. Without proper inventory planning systems, companies might face a lot of hardships such as overstocking, shortages/out-of-stocks, wastage, and so on. Inventory planning ensures that the current trends are considered to ensure enough stock is present to meet consumer demand, and a warning is issued before a shortage occurs.
The Inventory in hand is converted into revenue once it is sold, but before that, the inventory is locked up as capital. Thus, keeping too much of stock in inventory is expensive to the company and minimizes cash flow. A business never wants to stock more than they sell, and poor inventory turnover can result in unsold or dead stock.
Benefits of Inventory Stock Planning
Inventory planning ensures businesses can fulfill orders at the right time and increase their profit margins. Inventory planning also helps in:
- Saving Money – Comprehending stock patterns lets you see how much and where you have something in stock in real-time to utilize the stock better. You can keep less stock at each location as you can predict forecasts beforehand, minimizing the cost locked up in inventory. It also minimizes the amount of stock wastage before the stock is sold.
- Satisfies customers – Customers want orders to be fulfilled without having to wait. One way to ensure customer loyalty is to ensure they get the items immediately when they want them.
- Enhances Cash Flow – With the right inventory planning software, you can spend money on sales inventory, so cash flow is smooth.
Challenges in Inventory Planning
The major challenge of inventory planning is either having too much of slow-moving products in inventory or not having enough items for satisfying orders. Apart from that other hindrances include not knowing how much inventory you have in stock and where they are located in the distribution centers. Some of the other challenges include:
Poor Processes –
Manual or traditional processes can fill the operations with mistakes and slow down the entire process.
Fluctuating Consumer Demand –
Consumer behavior is subjected to constant changes, and if the inventory planning software cannot analyze trends, you will not be able to comprehend consumer fluctuations.
Obtaining Correct Stock Details –
When you do not have the correct stock estimations for the future, you would not know when to order for replenishment, which products are in high demand, and which products you should avoid stocking.
Utilizing Storage Spaces Well –
Employing staff is no good if you cannot locate where the stock is located. Inventory planning systems need to give real-time insight into where the stocks are located in the warehouse.
Inventory Management Hacks
Inventory management is a complicated process for large & small organizations alike and companies need to constantly explore multiple hacks in order to improve drastically. Let’s have a look at the various inventory management techniques:
- Minimum Order Quantity is the minimum level of inventory an organization should buy to keep expenses low. Inventory goods with higher production costs have smaller minimum order quantities compared to inexpensive items that are easier to produce.
- Economic Order Quantity is a formula for the amount of inventory an organization should purchase with a set of factors such as demand rate, the total cost of production, and so on. The formula determines the maximum number of units to reduce holding, buying, and other expenses.
- Just-in-time Inventory is a method in which organizations obtain inventory as and when needed rather than stocking the inventory with excess goods and locking up revenue in dead stock.
- ABC Analysis – Inventory goods can be categorized into Category A, the fastest-selling product, Category B products have average demand, and Category C products have the lowest demand.
- Safety Stock Inventory is the additional inventory ordered and kept aside if an organization does not have enough for replenishment. It assists in preventing stock-outs because of inaccurate forecasting or unanticipated changes in consumer demand.
- Reorder Point Formula estimates the minimum stock level that a business should have before ordering for replenishment. A reorder point is usually higher than the safety stock.
- Dropshipping is an order fulfillment process in which products are directly shipped to customers by the supplier. When an item is sold, the business purchases it from the supplier and ships it to the customer.
Kronoscope by Fountain9 is a robust inventory planning system that automatically places replenishment orders when the reorder point is reached. It also gives staff real-time insight into the different warehouses across all the distribution channels. You can maintain an optimum inventory level with the software to meet consumer demand at the proper time, making customers keep coming back to you.