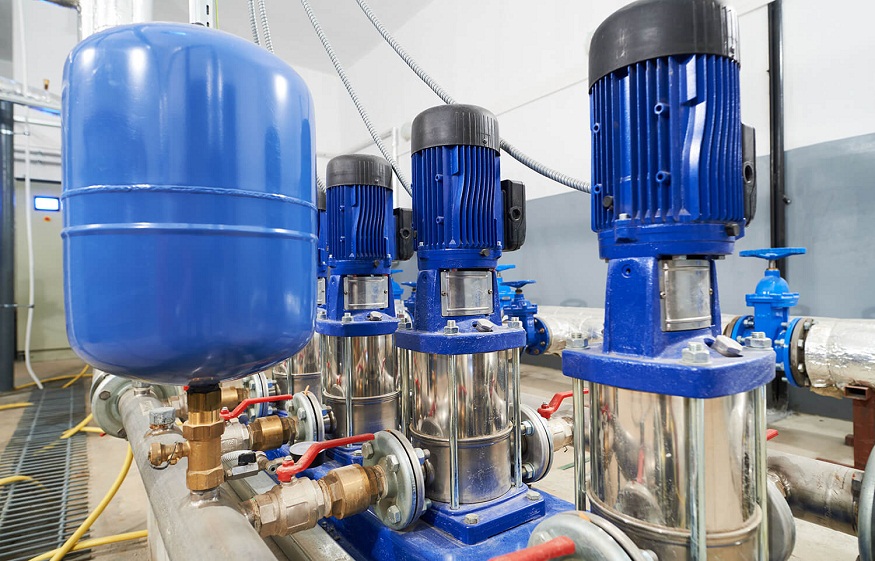
Keeping maintenance costs low is a constant battle in heavy-duty manufacturing industries, where efficiency, reliability, and durability are critical. Progressing cavity pumps (PC pumps), known for their versatility and robust design, are increasingly valued for reducing downtime and minimizing upkeep expenses. But how do these pumps work, and what makes them so effective in high-demand environments?
This article explores the role of progressing cavity pumps in heavy-duty manufacturing, the unique benefits they offer, and how they can become a game-changer for your operations.
What Are Progressing Cavity Pumps?
Progressing cavity pumps, often shortened to PC pumps, are positive displacement pumps designed to transfer fluids of varying viscosities and consistencies. These pumps are particularly effective for moving shear-sensitive and abrasive materials, making them indispensable across manufacturing, oil and gas, chemical processing, wastewater treatment, and even food production industries.
How Do PC Pumps Work?
At the heart of the PC pump is a helix-shaped rotor that rotates within a stator, forming cavities that progress from one end of the pump to the other. This design creates a consistent flow that can handle even highly viscous or abrasive substances, which might clog or damage traditional pump systems.
Their simplicity in structure—fewer moving parts and a robust build—renders them durable and easier to maintain than alternative solutions, such as centrifugal pumps.
Key Benefits of Progressing Cavity Pumps in Heavy-Duty Manufacturing
When it comes to heavy-duty manufacturing, efficiency and cost-saving solutions are essential. Progressing cavity pumps stand out for several reasons that directly impact operational costs.
1. Reduced Maintenance Requirements
Unlike traditional pumps with more complex systems, PC pumps have a straightforward design with fewer components, which naturally reduces wear and tear. The rotor and stator, their two primary working parts, are engineered for durability even in the harshest conditions.
This durability means fewer mechanical breakdowns, lower replacement part costs, and reduced reliance on emergency repairs—key factors in keeping maintenance budgets manageable.
2. Extended Lifespan with Less Wear
PC pumps are built to handle abrasive and highly viscous materials without wearing down quickly. Their gentle pumping action creates less stress on components, resulting in an extended lifespan. For industries routinely dealing with challenging substances—such as sludge in wastewater plants or viscous oils in manufacturing facilities—this capability ensures smoother operations over time.
3. Energy Efficiency and Consistent Performance
Progressing cavity pumps maintain consistent flow rates, even when handling materials that vary significantly in density or viscosity. This consistent output reduces energy consumption compared to pumps that struggle under changing loads, ensuring operational efficiency for heavy-duty applications.
Compared to centrifugal pumps, which can lose efficiency under non-optimal conditions, PC pumps excel at steady-state operations, minimizing energy wastage and maximizing ROI over time.
4. Versatility Across Applications
One of the defining advantages of PC pumps is their ability to handle a wide variety of materials. Whether it’s transporting delicate food products, reactive chemicals, or heavy sludge, PC pumps adapt to the task at hand without compromise.
For manufacturers handling diverse requirements, this versatility reduces the need—and cost—of separate specialized equipment for different functions.
Why Reduced Maintenance Costs Matter in Heavy-Duty Manufacturing
Maintenance costs are more than just a line item on a balance sheet; they directly impact productivity, profitability, and customer satisfaction. Here’s why minimizing these expenses is vital:
- Reduced Downtime: Every minute a production line is down results in lost revenue. Equipment that requires frequent maintenance can lead to significant operational delays.
- Lower Spare Parts Expenses: Complex machinery can dramatically increase spare parts costs. Progressing cavity pumps’ simpler design reduces such burdens.
- Optimized Labor Allocation: Instead of assigning workers to repetitive or unexpected maintenance tasks, they can focus on higher-value, strategic activities.
By integrating PC pumps into your manufacturing process, your operation benefits not only from lower costs but also from better resource utilization and improved workflow efficiency.
Best Practices for Maximizing the Benefits of PC Pumps
While PC pumps are inherently efficient and durable, leveraging their full potential requires proper implementation and maintenance. Here are some best practices to consider.
1. Tailored Selection for Materials and Applications
Every manufacturing setup is different. Choose a PC pump optimized for the specific materials you handle and the conditions you work in. Consult with pump specialists or manufacturers to ensure compatibility with abrasive, shear-sensitive, or high-viscosity substances.
2. Routine Maintenance Protocols
Though PC pumps require less frequent maintenance, routine inspections are still crucial for their longevity. Focus on monitoring wear on the rotor and stator and ensure proper lubrication.
3. Operator Training
A knowledgeable team is essential for maximizing the performance of your PC pumps. Train staff on proper usage and troubleshooting practices to minimize operational errors that could lead to premature wear.
4. Partner with Trusted Suppliers
Work with reputable suppliers who can provide high-quality PC pumps, spare parts, and technical support. Their expertise ensures long-term reliability and returns on investment.
Is a PC Pump Right for Your Business?
There’s no one-size-fits-all answer, but for heavy-duty manufacturers, progressing cavity pumps often prove to be a valuable solution for transporting difficult fluids, reducing energy consumption, and slashing maintenance costs.
Whether you’re navigating challenges in oil refining, chemical production, or wastewater management, these pumps can serve as a reliable workhorse that ensures smoother day-to-day operations and long-term cost savings.
Transform Your Manufacturing Cost Efficiency Today
If high maintenance costs are bogging down your operations, it might be time to rethink your pumping systems. By integrating a progressing cavity pump into your workflow, you not only reduce costs but increase reliability and productivity.
For more insights, connect with our experts to explore tailored solutions for your manufacturing needs. Don’t wait—maximize efficiency, minimize downtime, and empower your operations with the reliability of PC pumps today!